Zapping manure with special electrode could produce fertilizers, other chemicals
Analysis suggests system could reduce ammonia emissions from a large dairy by more than 50%.
December 22, 2023
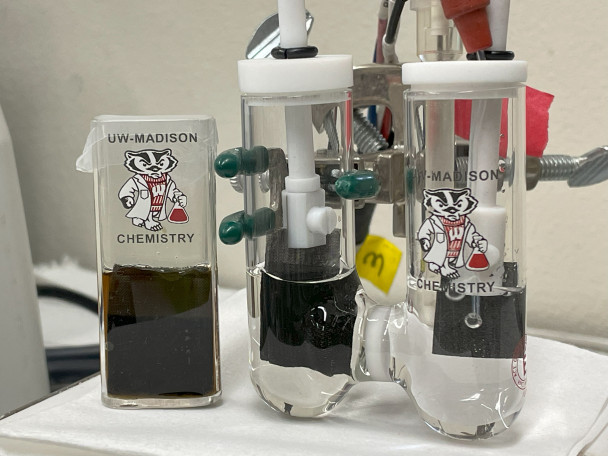
An interdisciplinary team led by University of Wisconsin–Madison scientists has developed a new technique that could help farmers extract useful nutrients such as ammonia and potassium from livestock manure to efficiently make fertilizer and other useful chemical products.
While the strategy still needs to be scaled up beyond a proof-of-concept stage, the group’s preliminary analyses show it could offer considerable benefits by cutting water and air pollution while simultaneously creating products that farmers could use or sell.
Manure stinks in part because it contains ammonia, one of the more than 300 compounds that contribute to its odor. The pungent gas is not only a harmful air pollutant but can turn into the greenhouse gas nitrous oxide and water-polluting nitrate.
Ammonia is also the foundation of many nitrogen fertilizers that have fueled modern crop production. The industrial method for making ammonia for nitrogen-based fertilizers, the Haber-Bosch process, consumes a lot of energy and emits hundreds of millions of tons of greenhouse gasses every year.
Although manure itself can be used as fertilizer, doing so can be costly, logistically challenging and has environmental drawbacks. So, researchers around the world are hunting for strategies to efficiently recover ammonia from manure, creating more concentrated and valuable fertilizers that are greener and more affordable to transport.
Among these strategies are chemical processes driven by electricity, which is becoming increasingly inexpensive in many rural communities thanks to growing solar and wind power generation. However, most electrochemical techniques in development are not yet practical, mainly because they consume a lot of energy and aren’t efficient enough at pulling dissolved ammonia (in the form of ammonium ions) out of manure.
This new technique, described in a paper published in the journal Nature Sustainability, relies on a specially designed electrode, like those used for batteries, that targets ammonium ions.
The technique involves a nickel-based electrode that is placed directly into the manure wastewater. As organic matter in the manure naturally gets oxidized by the electrode, the ammonium, as well as potassium ions, within the wastewater are selectively driven into and captured by the electrode.
The strategy does not end with simply removing the nutrients from the wastewater.
In an innovative step that could help make the process even more attractive, the nutrient-loaded electrode is then placed into a device that uses electricity to release the recovered ammonium and potassium ions, which can then be used to make nitrogen and potassium-based fertilizers, and simultaneously produce other useful chemical products. These could include hydrogen fuel or hydrogen peroxide, which is commonly used for disinfection.
“We got lucky because nature does a lot of the work for us,” says Song Jin, a UW–Madison professor of chemistry who led the work along with doctoral candidate Rui Wang and civil and environmental engineering Professor Mohan Qin.
“Manure has all this stuff in it, and we don’t have to do too much extra work,” Jin says. “The battery material goes in, and ammonia gets sucked out when the organic stuff gets oxidized.”
Trial runs with small amounts of manure recovered more than half the ammonia in the first pass, with a recovery of about 85% after two cycles.
The ability to produce fertilizers and other chemical products together is a key part of why the team believes their strategy could be a winner. An environmental analysis led by Rebecca Larson, a professor in the Nelson Institute for Environmental Studies, indicates that a 1,000-head dairy farm operation could reduce its ammonia emissions by more than 50% by deploying the system, while also significantly reducing the amount of nitrate entering nearby waters.
Meanwhile, a preliminary technical economic analysis led by Professor Fikile Brushett, a collaborator at Massachusetts Institute of Technology, shows that a model dairy farm using the system could expect resulting revenues to be higher than operating costs, so long as electricity prices aren’t exorbitant.
The next steps include further improving the materials and processes, scaling the system up and studying how it functions at a level more closely resembling a real-world livestock operation. Jin is optimistic that the system’s benefits will continue to outweigh potential costs at these larger scales, given the initial analyses.
“It looks indeed to be promising,” says Qin. “There’s a pathway to see how this might really help in the real world.”
This research was supported by the National Science Foundation. A provisional patent on this technology has also been filed by the Wisconsin Alumni Research Foundation (WARF).
You May Also Like