Hog Reproduction
thumbnail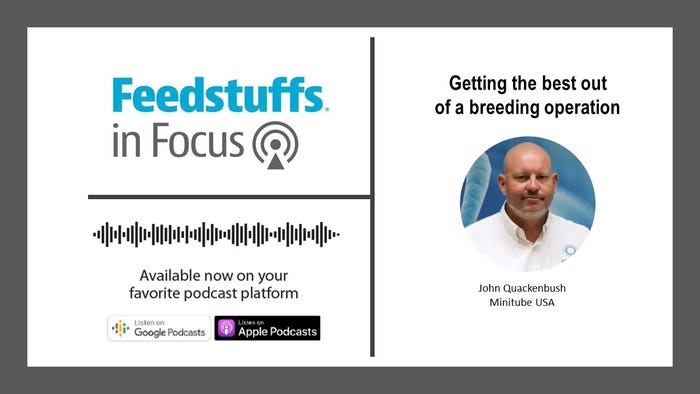
Livestock Management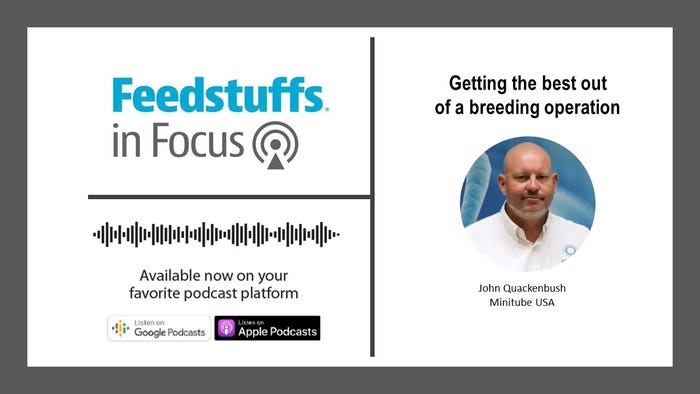
Getting the best out of a breeding operationGetting the best out of a breeding operation
What does it take to get the best out of a breeding operation? John Quackenbush of Minitube joins us with some tips.
Subscribe to Our Newsletters
National Hog Farmer is the source for hog production, management and market news