Hog Health
thumbnail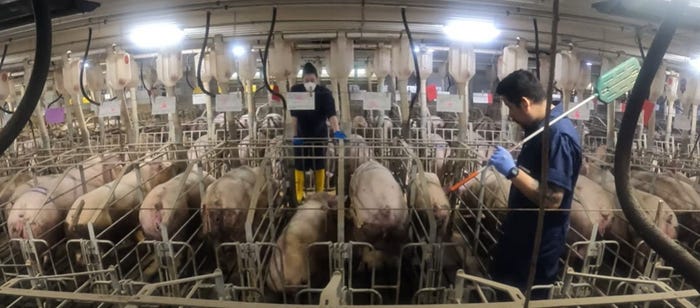
Livestock Management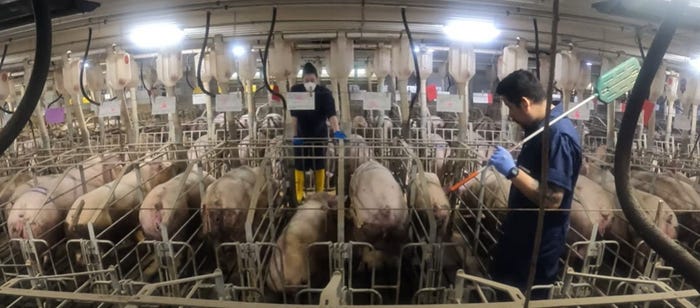
Take a practical approach to reduce sow mortalityTake a practical approach to reduce sow mortality
Iowa Pork Industry Center offers an SOP for caretakers to use while conducting their daily observations.
byAnn Hess
Subscribe to Our Newsletters
National Hog Farmer is the source for hog production, management and market news