Hog Building Designs Help Mitigate Environmental, Energy Concerns
Great strides have been made in the designs of animal and poultry production facilities over the last 40 years. Many labor-intensive chores have been automated. In many cases, the automatic climate control systems in livestock barns are better than what we have in our homes
April 15, 2010
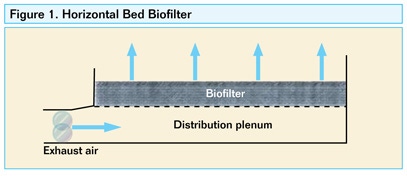
Great strides have been made in the designs of animal and poultry production facilities over the last 40 years. Many labor-intensive chores have been automated. In many cases, the automatic climate control systems in livestock barns are better than what we have in our homes. The computing capacity in those systems far exceeds the capability of the on-board computing systems that put man on the moon.
Still, in today's political climate, producers face concerns about community health, gas and particulate emissions and their influence on global warming, carbon credits and animal welfare. But it's times like these that foster a climate of innovation and the potential for cost-effective retooling. With that thought in mind, let's address some of these issues related to swine housing.
Ventilation Challenges
Modern ventilation and environmental management systems are sophisticated and automated — ranging from complete natural ventilation to complete mechanical ventilation — with most any combination in between. These advances provide a rearing environment in which animals can achieve their genetic potential.
It is to the producers' advantage to develop as stress-free of an environment as possible to achieve maximum production efficiency — a detail that the animal rights community has never fully appreciated.
Our ability to control and automate housing systems will allow researchers and producers to face the political challenges ahead. Efforts are underway with the U.S. Environmental Protection Agency, for example, to establish emission factors for animal and poultry production systems — a final outcome of the National Air Emissions Monitoring Study that was recently completed (see https://engineering.purdue.edu/~odor/NAEMS/index.htm).
Emission factors for ammonia, hydrogen sulfide, carbon dioxide and particulate matter will be front and center. Although it's unclear how these emission factors will be used, it appears likely those results will be used to establish emissions limits (on-site animal unit limits), which, if above an established threshold, will force producers to decide whether to reduce animal density, apply a mitigation strategy, modify an existing building or prove the regulators wrong.

Emission factors and regulated limits of selected gases and particulates will be a reality in the future, and the future is clearly in sight.
How should a building be designed to address the issues surrounding barn emissions?
At the outset, a proposal to mitigate all air emitted from the housing system is unrealistic. If the pork industry ever gets to the point where regulations require complete mitigation, the time to throw in the towel will have arrived.
Instead, with modest changes to a ventilation system and building design, many of the emission standards that I foresee could be addressed quite well. Here are some options:
Emissions mitigation
The research community is working hard to develop low-cost options to mitigate gas and particulate emissions, if required, and biofiltration is the best available technology. Variations in designs include horizontal bed biofilters (Figure 1) and vertical biofilters (Figure 2), with variations in media content from 100% wood chips to combinations of wood chips and compost materials. With suitable media moisture content (50-60% wet basis) and contact times (3-5 seconds), rather impressive mitigation efficiencies for ammonia, hydrogen sulfide and odor can be attained. More details regarding biofilter design can be found by contacting Dick Nicolai at South Dakota State University (http://agbiopubs.sdstate.edu/articles/FS925-C.pdf).
Biofiltration requires fan-exhausted air, add-on equipment to the ventilation system, extra fan energy expenditure, extra management and extra control, but it is still the best strategy available for emission mitigation.
To be clear, however, mitigation of all animal housing ventilation air is impossible. Not only is it unrealistic in terms of biofiltration size requirements, but the sheer amount of ventilation air is too large to mitigate.
For example, during the summer months we routinely flush the air from our barns, via the ventilation system, at a rate of about 100 fresh-air changes per hour (ACH). In a typical 1,000-head finisher, this amounts to about 120,000 cu. ft./min. (cfm) or about 2,000 cfm/sec. This is approaching an air-volume equivalent of scrubbing a 16 × 16 × 8 ft. room in your home every second!
Another novel idea for controlling emissions being studied is ultraviolet destruction of gases and odorous compounds. Still in the laboratory testing phase, the initial results are very promising. Ultraviolet technology is also being tested for its efficacy in controlling viruses riding the air inlet stream. To date, the destruction of targeted viruses has been equally impressive. Field trials are at least two years away, with many hurdles to overcome; but if successful, it could prove to be an effective mitigation method.
The very best way to handle source emissions of any kind is to target the source vs. the “post-processing” methods described above. Feeding regime modifications will be a key component with barns of the future. Researchers around the globe are working to meet the energetic demand of today's pig, while reducing emissions of odors and targeted gases.
Ventilation for the occupants, not the manure
Effective mitigation of gases and odors is a trade-off between method used, effectiveness and cost. If housing systems can be designed to separate the ventilation needs of the pigs and the exposed manure, a significant reduction in mitigation cost could be realized.
Deep-pit designs, for example, are attractive on paper due to the reduced footprint of an entire operation, plus the nutrient value of the manure as a fertilizer resource. However, when considering the mitigation needs of deep-pit facilities, the concentrations of gases and odors can be high, requiring potentially costly mitigation methods.
If deep-pit housing systems could be designed so the manure-holding tank is ventilated separately from the animal needs, a vastly reduced volume of air would be needed, thereby reducing the cost of mitigation, the size of mitigation method and the overall cost, while still improving the indoor air quality for the animals and workers.
This concept has been tested in the United States and Europe, where the area below the slotted flooring has been modified. An example is a V-shaped scraper system with ready removal of feces and urine, which minimizes the manure and gas zone exposure.
Another option being tested at Iowa State University is a modified subfloor for deep-pit facilities (Figure 3). With this concept, the slotted flooring remains unchanged to allow for ready flow of manure and urine into the holding tank, away from the animal zone. The holding tank provides a captive, separated “room” for ventilating on a much smaller scale than is necessary for the animals in the barn.
With subfloor strategies, the biggest requirements are methods to prevent manure buildup on the subfloor and the ability to ventilate the manure-holding area at a rate that allows for a steady downdraft of room air into the holding area, thereby preventing back-gassing into the animal-occupied zone.
These features would have to be designed into new construction and would require added pit depth to accommodate the subfloor. But the design would undoubtedly improve the quality of occupied room air and provide a method for mitigation via the exhausted airstream that demands much less volume than that required for animal needs.
Reducing the influence of the ventilation system on manure emissions
Subtle changes to ventilation and housing design can have an impact on manure emissions. For example, increased airspeeds and warmer manure temperatures will increase volatilization of emissions, especially ammonia, to the atmosphere. Cooling manure or manure-exposed surfaces and preventing high airspeeds across the manure surface will reduce these emissions. Geothermal cooling of the manure is expensive, but reducing airspeeds over manure-exposed surfaces could be considered in future designs.
Smarter, impact-based emissions control
For many emissions-reduction policies, the easy answer is to mitigate all exhausted air, all of the time. Again, such a policy must be resisted at all costs. There are methods available to reduce emissions to satisfy regulatory constraints, while simultaneously reducing nuisance impacts to the surrounding community.
Impact-based emissions control is being considered by researchers. For example, we know that odors and gases, in general, can travel longer distances when atmospheric conditions are stable, typically experienced during early evening, evening, and early morning during the summer. With a stable atmosphere, vertical dispersion is low relative to horizontal dispersion.
An impact-based mitigation control strategy during these more stable atmospheric conditions makes sense from an odor nuisance control viewpoint and, simultaneously, will result in a reduction in the gases that are targeted for future regulation. Furthermore, in many Midwestern summer climates, outside temperatures drop enough during the evening so ventilation needs of the animals are reduced, in many cases, to half or less of the ventilation requirements in the heat of the day. If the ventilation system is designed accordingly, nearly all of the “highest impact” emitted air will be mitigated to half or below the total volume of air designed for the building. This is beneficial to the producer and the surrounding community.
This ongoing research shows promise as a viable strategy. Control systems will be required to handle this logic, and on-site weather stations will be needed to assess atmospheric stability, but these are relatively low-cost add-ons compared to mitigating all ventilation air from a housing system.
Energy Management
Energy management will continue to be a key component to the success of a housing design. Following are several considerations intended to reduce a barn's environmental footprint and ultimately improve production efficiency:
Zone control in barns
One approach is to implement more microclimate control for energy-intensive components of a barn. Immature pigs in cold climates are a challenge. Heating and ventilating an entire building — designed for the most part for much higher animal densities — is costly. Therefore, controlling much smaller areas or microclimates makes sense.
Housing designs will need easy-to-manage microclimate zones. For example, hovers or creep-area volumes can provide very effective microclimate zone control, but making them a part of housing design is often an afterthought.
The microclimate zones represent one attempt to provide smaller zone control for weaned pigs in a common wean-to-finish barn. Whenever possible, smaller controlled zones should be designed as part of new construction along with control systems that allow for two-climate control levels — one for the cooler, less susceptible macroclimate, another for more sensitive microclimate control. Controller technology is currently available to accommodate dual-climate control, but logic needs to be placed in these controllers, synchronized with building design features.
Minimum ventilation
All too often, barns are over-ventilated during cold, minimum ventilation periods. This is easy to do because there is a fine line between just-enough minimum ventilation and excessive minimum ventilation.
Heating of minimum ventilation air is a large energy consumer. For example, if a 1,000-pig barn is mistakenly over-ventilated by 1 cfm/pig during the heating season and the mistake persists for four months (2,880 hours) with a 50°F temperature difference (70°F inside, 20°F outside), the excess propane used would approach 2,000 gallons. Of course, this is an exaggeration, but it illustrates that the impact of minimum ventilation is enormous. Taking the time to have a trained engineer review your ventilation system often pays large dividends.
Controlling air leaks
Wind is a powerful ventilation force that can provide tremendous hot weather ventilation benefit, but it also can be an enormous hindrance during the heating season.
For example, a sidewall curtain with three, 4-in.-diameter mouse holes will allow about 40 cfm of infiltration air into the barn when subjected to a 5- mph wind. Again, if the situation persists for the 2,880 hours (four months), an additional 80 gallons of propane would be needed to heat the air to an acceptable room temperature.
Other things, such as curtain overlaps, end pocket seals, etc. are also sources of air leakage that add up to be expensive propane users. Detecting and fixing them would be a bigger benefit than talking to your local rural electric cooperative about installing wind turbines or solar panels.
I recommend curtain overlaps of 3 in. to minimize air leakage through the barn curtain. This requires routine fall and winter inspections as cabling systems will change over time.
Set-point temperature maintenance
In general, we keep barns too warm during the heating season. Take some time to adjust your set-point temperature. Ramp it down until pig behavior tells you that you have gone too far (e.g., huddling, piling, etc.). Pigs are our very best sensors.
Every barn has different features like cold walls, cold curtains, infiltration and drafts caused by the ventilation system, but once the set point is established, it will pay big dividends. There is no such thing as a single recommended set-point temperature/ramping scheme for pig housing.
Simple issues like temperature sensor placement relative to pig level, heater capacity, and inlet systems all affect the ideal ramp for a barn. And, from a controller manufacturer's perspective, providing a diurnal ramp feature synchronized with the overall ramp as a function of pig age is an option that producers should consider. We should adjust barn set points just as we do in our homes.
Heat recovery
Engineers and on-farm innovators have tried for years to recover heated ventilation air before spilling it into the environment. Dust, gases and moisture combined make this a big challenge. The very best attempt at this is the Airworks® Building System (http://www.whiteshirehamroc.com/airworks.html), where heat recovery is a large component of a specialty barn design and ventilation system. As a research community, we need to do a better job of exploring more options for heat recovery.

Alternative Energy Sources
It is easy to say that animal housing systems should implement solar, wind, and anaerobic digestion systems as alternative energy sources. It is not so easily done.
With most alternative energy considerations, the biggest challenge is storage of energy to provide a stable and continuous source. I do not believe we are ready to use solar or wind energy sources in swine housing systems. Effective research would require a testing site dedicated to alternative energy options and designs into pig housing. Nonetheless, let's discuss the potential for wind, solar and anaerobic digestion for pig housing briefly:
Solar energy
Again, using a 1,000-head finisher, an average electrical consumption for fan power would be about 1450 kWh/month or 17,400 kWh/year. This assumes a monthly average ventilation rate of 30 cfm/pig and an average fan efficiency of 15 cfm/W. To provide solar energy and the associated storage to operate the fans in central Iowa, the solar collector size would be about 1,500 sq. ft. This assumes four 4 kW photovoltaic (PV) array grids (a common PV array incremental size) at 377 sq. ft./array located in Des Moines, and takes into account transfer efficiencies from the DC-generated array to output AC power. Figure 4 summarizes the estimated monthly and annual total for a single 4 kW PV array system. Different locations and scenarios can be estimated at http://rredc.nrel.gov/solar/calculators/PVWATTS/version1/.
For a PV array of this type, the estimated cost, less installation, would be roughly $5/watt or about $80,000 for the 1,000-hd finisher (http://www.infinitepower.org/pdf/FactSheet-24.pdf).
Probably the best application of solar energy is passive use in winter to provide microclimate energy needs. For example, sidewall curtain materials could readily allow solar radiation to pass through, while retaining the absorbed solar energy within the barn, stored passively in the surrounding concrete flooring. Solar domes, currently used in homes to reflect and concentrate solar energy into prescribed locations, such as microclimate application for small pigs, is another potential application.
Passive solar designs have not been well tested for pig housing and, although the overall influence would be small, when coupled with other methods such as geothermal cooling/heating of the concrete mass inside barns, is a viable option. Again, more research in pig housing is needed.
Wind energy
With wind farms popping up all over the country, especially in the upper Midwestern states, it seems reasonable that wind cooperatives could be established to provide electrical energy needs for pods of livestock producers.
Again, using the 17,400 kWh annual energy requirements for a 1,000-head finisher, a 10-kW turbine elevated to about 130 ft. would be needed to produce about 26,000 kWh in central Iowa (See Figure 5 for annual, monthly potential). Cost of equipment, including turbine, tower, battery storage and distribution equipment would be in excess of $50,000. More information can be found at http://www.energy.iastate.edu/renewable/wind/assessment/index.htm.
Undoubtedly, the very best use of wind in terms of pig housing is to utilize natural ventilation with curtain-sided buildings. If your region has less than 5% calm periods in the heat of summer, natural ventilation is a fantastic direct and free use of alternative energy.
Again, using the 1,000-head finisher example, we can gain a better idea of wind's potential for natural ventilation. During the heat of summer, about 100-120 fresh-air exchanges per hour (ACH) are needed to keep inside temperature relatively close to the outdoor temperature, without supplemental evaporative cooling. If the barn is oriented perpendicular to predominant summer winds and both sidewall curtains are open 4 ft., the barn would be ventilated at about 120 ACH with a nominal 2-mph wind. Clearly, the power of wind to ventilate is far and away the best way to harness this alternative energy source.
In fact, the concern often is not whether enough air can be moved through the barn, but rather preventing drafts on young pigs. For small pigs, a quick-response control system is needed to respond rapidly to changing weather patterns.
Anaerobic digestion
Anaerobic digestion is an option that has been bantered around for many years. The technology and equipment used for digestion, gas capture and conversion to electricity has advanced tremendously over the years. However, the mechanical and management requirements to make anaerobic digestion successful, combined with a steady and sufficient feedstock supply, remains challenging.
Roughly 65% of the biogas generated from animal manure is methane, a powerful greenhouse gas. Flaring or utilizing on-farm methane for heating or electricity generation reduces this greenhouse gas significantly.
USDA researchers developed a comprehensive means of estimating the economics and feasibility of anaerobic digestion for specific applications. For more information, see: (http://www.abe.iastate.edu/fileadmin/www.abe.iastate.edu/extension/wastemgmt/Anaerobic_Digestion).
The data on anaerobic digestion is quite scarce and with large variations. Hopefully, active research will help advance this technology for ready on-farm use.
Futuristic Building Designs
Efforts to promote more environmentally friendly methods of pork production are underway. In many respects, more stringent regulations on ammonia have pushed European efforts ahead faster than the Americans. Three examples:
Green label barns
In the '90s, the Dutch offered pork producers incentives to implement barn design features that would reduce ammonia emissions by 50% by 2000 and by 70% by 2005, compared to 1980 emission levels. Mandatory provisions included covering outside manure storages and implementing barn design and feeding changes. A Green Label certification was given to those who achieved emission reduction targets.
Certified barns were proven to reduce emissions by 40-60%, depending on pig size and associated housing, and incorporated manure removal, manure pH adjustment and manure cooling. Certified producers received tax incentives and protection from further regulation for 15 years.
U.S. Green Pig Barn project
University of Minnesota Agricultural Engineer Larry Jacobson is spearheading a Green Pig Barn initiative targeting energy conservation, manure management and ventilation strategies that minimize a barn's environmental footprint. Suggested strategies from this ongoing research effort are anticipated within the next year or so. Further details can be found at (http://www.mnpork.com/producers/2009/PorkCongress09/environmentalfootprint09.pdf).
Mission 2050 research and teaching complex
Vern Osborne at the University of Guelph has aggressively spearheaded an effort to construct a research and teaching facility dedicated to futuristic building designs. Mission 2050 is intended to develop a research station near the University of Guelph, where emissions reduction and renewable energy implementation in animal agriculture are the focus. Once completed, this complex will serve as an incubator for researchers worldwide to test out-of-the-box concepts for future adoption on the farm. For more details, go to (http://www.londonswineconference.ca/proceedings/2008/LSC2008_VOsborne.pdf).
Cost Recovery the Key
The U.S. pork industry is staring directly in the face of regulation. It is vitally important that legislators and regulators are made aware of the dire consequences that blanket policies for environmental mitigation could have. It is almost impossible to ask producers to implement added costs for mitigation, as currently no economic strategies exist for them to recover these costs. The U.S. consumer must be willing to spend more for proven, environmentally friendly designs, and this added revenue must somehow find its way back to the producer.
The research community must work with builders to develop and test housing designs that have proven mitigation values. Producers need a method to verify and validate site-specific emissions to confirm that mitigation is needed and that there is a reasonable assurance of payback for the effort.
Energy conservation and the use of alternative energy will find its way into pork production in subtle, yet important ways, such as microclimate control. Using wind for natural ventilation has always been the biggest alternative energy source. However, expecting alternative energy to fuel mechanical ventilation needs is unrealistic.
Conservation is far and away our best strategy for reducing our dependence on fossil fuel energy use and for tempering the discussion about the need for alternative energy sources.
Hiring a third-party engineer to inspect facilities for opportunities in energy savings is usually money well spent. Often, the payback on such an investment can be measured in months rather than years.
You May Also Like